Topolový lustr
Určitě znáte ten pocit, ležíte doma po dlouhém a náročném home office, venku je mrazivo a dávno tma a vy si říkáte, že to světlo na stropě nějak není ono, málo svítí a chtělo by to změnu. Hned tedy otevřete na telefonu Pinterest a zadáte heslo „laser cut lamps“. A nový projekt je na světě.
Použité stroje
- Speedy 400
- Ruční vibrační delta bruska
Použitý materiál
- Topolová překližka tl. 4 mm
- Brusné papíry 120 a 240
- Bakelitová žárovková objímka E27
- Textilní dvoužilový kabel 2×0,75
- LED žárovka E27
- Volitelně: zástrčka do zásuvky, baldachýn, WAGO svorky
Stručný postup
- Příprava grafického návrhu pro řezání.
- Testování vůle mezi jednotlivými částmi.
- Vyřezání na laserové řezačce a obroušení v mechadílně.
- Sestavení konstrukce lustru.
- Zapojení kabeláže.
Design
Pro výrobu na většině strojů ve FabLabu potřebujete digitální data. V případě laserové řezačky se jedná při řezaní o vektorovou grafiku, při gravírování si poradíte i s grafikou rastrovou. Data si standardně můžete opatřit třemi způsoby: sami si je připravíte, bezplatně si je stáhnete z internetu, nebo si je koupíte. Já se rozhodnul pro tento projekt data koupit, konkrétně z platformy Etsy. Data pro tři modely lustru a dvě tloušťky materiálu mě stála necelých 70 Kč. Největší nevýhodu takto koupených dat vidím v tom, že pokud bych chtěl design lustru lehce upravit nebo použít jinou tloušťku materiálu, musel bych grafiku složitě upravovat ručně. V tomto případě naštěstí stačilo zakoupená data už jen jednoduše upravit nastavením správných barev a tlouštěk čar v Illustratoru a optimalizovat polohu jednotlivých dílů tak, aby se vlezly na mnou použitý rozměr 4mm topolových překližek 500×400 mm, standardně dostupných na e-shopu FabLabu.
Btw. Jakmile jsem projekt dokončil, nedalo mi to a lustr s jiným designem jsem si sám vymodeloval ve Fusion 360. Většina rozměrů je v modelu nastavena parametricky, díky čemuž mohu pouhým přepsáním hodnot rozměry lustru jednoduše změnit. Hodí se to hlavně u tloušťky materiálu a hodnoty propalu, která ovlivňuje to, zda bude potřeba jednotlivé díly lepit nebo budou držet třením.
Materiál
Při volbě materiálu pro konstrukci lustru se mi nabízelo hned několik variant. Jasné bylo, že se musí jednat o dostupný materiál řezatelný na laseru. To zúžilo můj výběr na dřevěné překližky a plexisklo. Od začátku jsem měl v hlavě dřevo, proto jsem zvolil překližku, nicméně i lustr z plexiskla by mohl vypadat skvěle. Obavu bych měl pouze o snadno viditelný prach například na černém plexi. Výhodou by naopak bylo to, že by se jednotlivé díly již nemusely brousit. A třeba varianta lustru z opálového plexi? Překližku jsem volil z možností topol a buk. Jak už název napovídá, šel jsem nakonec do 4mm topolové překližky, a to ze dvou důvodů. Prvním bylo to, že lustr z topolové překližky bude lehčí, druhým pak to, že při řezání na laseru vzniká u buku výrazně větší opal na hranách. Zvažoval jsem i provozní bezpečnost použitého materiálu. Napadl mě pouze vliv tepla ze žárovky, ale vzhledem k tomu, že se dnes již v drtivé většině případů používají LED žárovky produkující minimum tepla, rychle jsem svoje myšlenkové pochody zastavil a řekl si, že to bude ok.
Zbytek dílů pro sestavení lustru jsem koupil. Při brouzdání internetem jsem objevil výrobce Creative Cables, který má ve své nabídce širokou škálu komponentů pro výrobu vlastních svítidel, a to včetně krásných textilních kabelů. Ale pro tento účel by posloužil i výrobek HEMMA z vy víte jakého obchodu. Koupil jsem bakelitovou objímku se standardní paticí E27, červený dvoužilový textilní kabel, plastovou průchodku a zástrčku do zásuvky. Zástrčku jsem koupil z toho důvodu, že jsem chtěl otestovat, zda bude lustr fungovat před samotným pověšením na strop. Pro bezpečné zavěšení na strop je potřeba koupit ještě baldachýn a pro snadnou instalaci WAGO svorky.
Výroba konstrukce lustru
Při řezání na laseru jsem si dával pozor na dvě věci. Abych měl s výrobou lustru po řezání co nejmenší starosti, snažil jsem se parametry řezání odladit tak, aby byl opal na překližce co nejmenší. Možností, jak se broušení úplně vyhnout, je předbroušení desek překližky oscilační bruskou na finální drsnost a poté její olepení papírovou maskovací páskou. To mi však v tomto případě přišlo neekonomické, opal je u měkčí topolové překližky navíc přijatelný. Kromě zdlouhavého broušení jsem se chtěl vyhnout i lepení konstrukce laseru. Jednalo by se o zdlouhavou činnost a místy poteklé lepidlo by pravděpodobně kazilo celkový estetický dojem z lustru. Při řezání dílů laserem přece jenom dochází k nějakému úbytku materiálu (u laserů ve FabLabu cca 0,1 mm, ale záleží na kombinaci konkrétního materiálu a parametrech řezání) a pokud chceme, aby díly držely pouze třením, je potřeba tento úbytek kompenzovat promítnutím pár desetin mm do rozměrů spojů. Před vyřezáním všech dílů, jsem se snažil tento balanc mezi spojitelností a soudržností najít postupnou změnou rozměrů drážek v žebrech lustru. Jako první jsem si tedy vyřezal horní a dolní prstenec a jeden kus žebra. Postupnou změnou rozměrů drážek se mi na třetí pokus podařilo najít optimální hodnotu. Odpad byl proto minimální, pouhá dvě žebra. Lustr se skládá celkem z 36 žeber, které však byly vyřezány za pár minut. Kdybych měl lustru vyrábět větší množství a z různých druhů překližky, určitě by se mi hodil jeho již zmíněný 3D parametrický model.
Po vyřezání všech potřebných dílů jsem se přesunul do mechadílny a brousil a brousil. Zhruba v půlce procesu broušení jsem přišel na to, že je možné brousit 3 žebra naráz a moje efektivita se výrazně zvýšila. U broušení horního a dolního prstence jsem si dal velký pozor na to, abych odstranil opravdu pouze jen opal a neodebral moc materiálu. Pokud by se tak stalo, bylo by moje předešlé ladění rozměrů k ničemu a musel bych prstence vyřezat znovu. Po obroušení všech dílů jsem se z nich snažil odstranit co nejvíce prachu pomocí smetáčku a vysavače. Dřevo jsem se rozhodl nijak povrchově neupravovat a nechat ho surové. Později jsem si uvědomil, že by asi bylo vhodné nějak dřevo zakonzervovat, třeba pomocí oleje na dřevo. Použitím oleje s pigmentem by z něj rázem mohl být třeba lustr z ořechu. Při psaní tohoto návodu mě napadá i to, že jednotlivá žebra by šla ještě klidně gravírovat.
Zapojení kabeláže
U laseru a v mechadílně se cítím jako ryba ve vodě, v blízkosti elektřiny s napětím 230 V spíš jako ryba na suchu, která brzo dostane elektrický šok. Ze zapojení kabeláže jsem měl respekt, ale po vyhledání relevantních návodů přímo od výrobce objímky a zástrčky jsem se do toho pustil. Nakonec to nebylo nic složitého a povedlo se mi zapojit jak objímku, tak zástrčku. Zde bych však rád upozornil, že připojení elektrických zařízení by měl provádět pouze odborník s příslušnými revizemi a pokud si nejste jistí, co děláte, rozhodně se do toho nepouštějte. Mohli byste dopadnout jako ta ryba na suchu s vážným elektrickým šokem a úrazem.
Budiž světlo
Jako zdroj světla jsem se rozhodl použít LED filamentovou žárovku imitující klasické vláknové retro žárovky, kterou jsem měl doma navíc. Rád bych ji ale v budoucnu vyměnil za nějakou větší a výkonnější. Lustr svítí, vypadá skvěle a hází parádní stíny. Zbytek projektu už musím dopracovat doma, vyměnit zástrčku za baldachýn a připevnit lustr ke stropu.
Pokud chcete mrknout na další moje projekty, můžete mě sledovat na Instagramu pod účtem @janwithbeard. Nebo si mě odchytněte přímo ve FabLabu!
V hlavních rolích
Laserová řezačka
Trotec Speedy 300 ti umožní řezat, gravírovat a značit dřevo, lepenku a plexisklo do tloušťky 8 mm o maximální ploše 726 x 432 mm.
Chci vědět víc >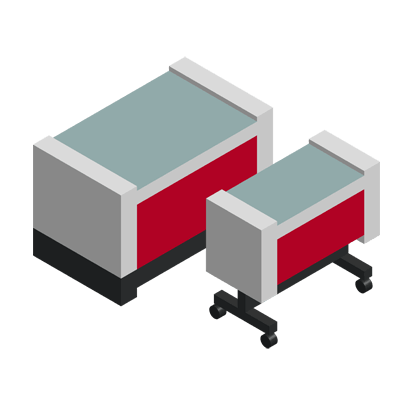
Sdílej projekt s ostatními Facebook na twitter